Time to read: 6 min
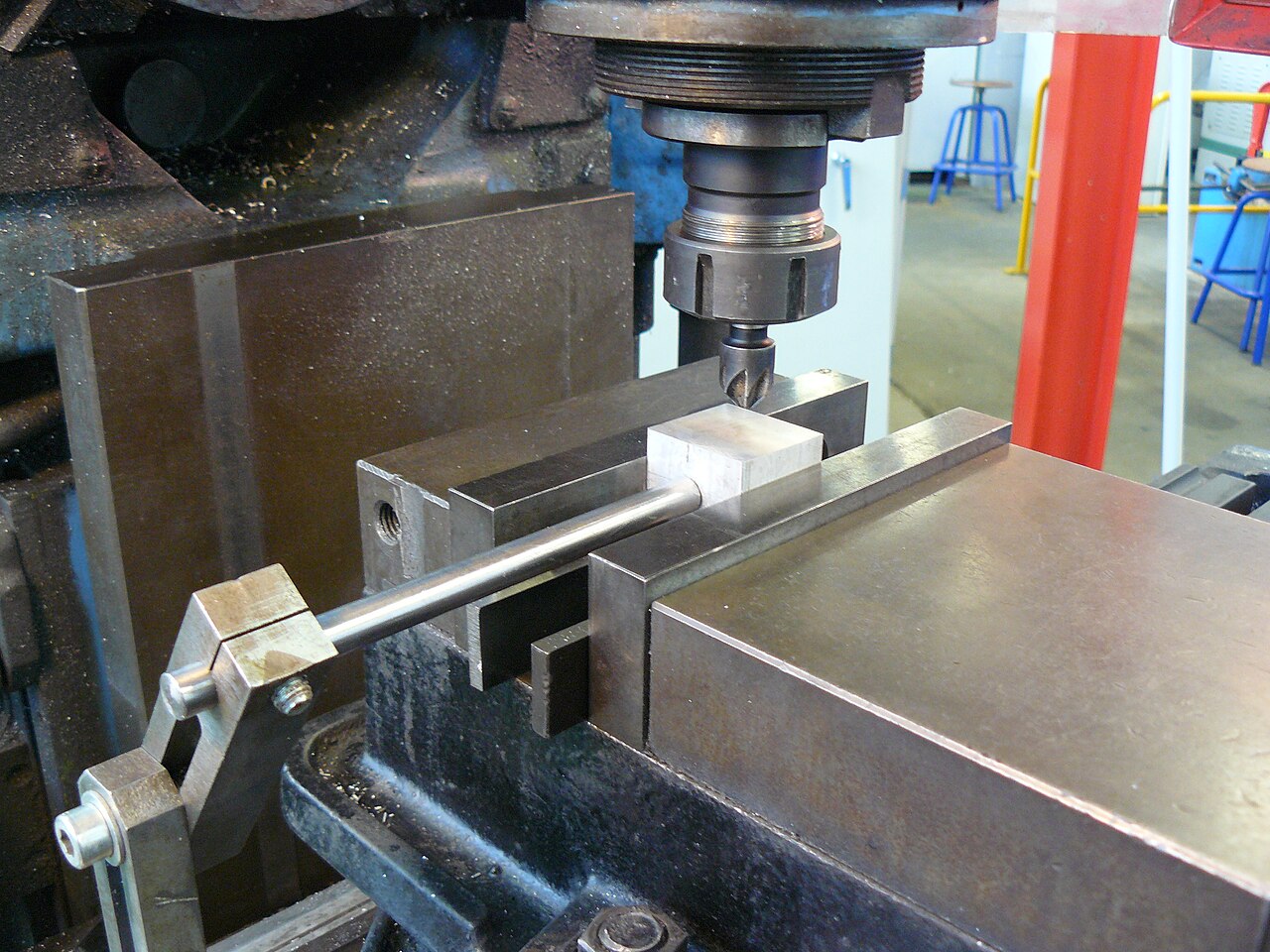
Milling: From Ancient Origins to Modern Precision
Milling is a versatile machining process with roots in food preparation. Initially, people used quern stones to mill grain into flour, employing a stationary stone and a rotating one with a central hole. This primitive setup laid the foundation for all rotating machinery. Today, milling refers to the use of rotating tool-cutting machines for various materials, including wood, metal, plastics, and stone.
Milling in Modern Manufacturing
In the manufacturing industry, milling is primarily used to cut materials from a workpiece, creating a wide range of items in different sizes and shapes. Milling machines are known for their precision and tight tolerances, which are crucial for industries where accuracy is paramount, such as aerospace. This sector often requires lightweight and complex parts for flight-engineered products, including airframe components, controls, and engine parts. Milling is also a popular choice for producing surgical tools and medical implants due to its ability to process biodegradable and easily sterilized materials.
Milling allows for the creation of intricate shapes and contours that would be difficult or impossible with other machining methods. A wide variety of materials can be machined, including metals like aluminum, steel, brass, and copper; plastics such as acrylic, Kevlar, polycarbonate, and nylon; and other materials like fiberglass, hardwood, ceramics, and glass.
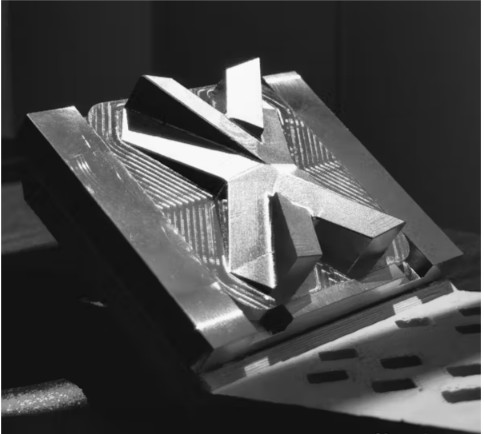
Advantages of Milling
The versatility of materials is just one of the many advantages of milling. It offers precision, high-quality finishes, and the ability to handle large workpieces. The process is quick and generates minimal waste, making it economical and easy to automate. However, milling may not be ideal for cutting hardened materials, and heavier cuts can take longer. The machines can be challenging to use and may require maintenance due to wear and tear. They also generate heat, chatter, and vibration.
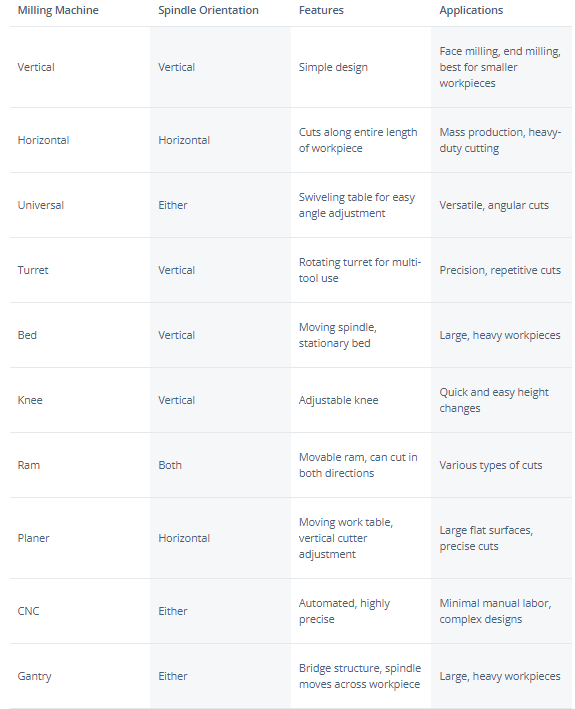
How Milling Works
At its core, milling involves a hardened steel or exotic material cutter rotating against the workpiece to remove material. Typically, the cutter moves on a fixed X-Y-axis but can also move on the Z-axis. A 3-axis milling machine is the most basic option, but 4, 5, and even 7-axis machines are available for more complex tasks.
The process begins by loading and clamping the workpiece securely to prevent movement during machining. Next, select the appropriate tool for the material and project. Set up the machine by adjusting parameters like spindle speed and cutting depth. Once everything is in place, you can start milling, either manually or through automation. Unofactory's team can provide examples of parts made using milling techniques.
Types of Milling Machines
There are numerous types of milling machines, each with its unique features and applications. Here are some of the most common types available through Unofactory's supplier network:
- Vertical Milling Machine: Features a vertical spindle and is suitable for face milling, end milling, and smaller workpieces.
- Horizontal Milling Machine: Cuts along the entire length of the workpiece, ideal for mass production and heavy-duty cutting.
- Universal Milling Machine: Offers a swiveling table for easy angle adjustments, making it versatile for angular cuts.
- Turret Milling Machine: Features a rotating turret for multi-tool use, perfect for precision and repetitive cuts.
- Bed Milling Machine: Designed for large, heavy workpieces with a moving spindle and stationary bed.
- Knee Milling Machine: Allows quick and easy height changes with an adjustable knee.
- Ram Milling Machine: Provides various types of cuts with a movable ram that can cut in both directions.
- Planer Milling Machine: Ideal for large flat surfaces and precise cuts, with a moving work table and vertical cutter adjustment.
- CNC Milling Machine: Automated and highly precise, minimizing manual labor and enabling complex designs.
- Gantry Milling Machine: Features a bridge structure with a spindle that moves across the workpiece, suitable for large, heavy workpieces.
Common Milling Methods
Climb and conventional milling are the two most widely used methods in manufacturing. Climb milling rotates the tool against the direction of the workpiece's motion, offering smooth surfaces and minimal material deviation. It is best for high-quality parts and thinner sections. Conventional milling rotates the tool in the same direction as the workpiece, making it suitable for more malleable materials and faster machining. However, it results in a rougher finish and increased tool wear.
Safety Precautions on the Factory Floor
When using milling machines, it is crucial to follow safety rules closely. A strict maintenance schedule helps identify potential hazards, such as damage, loose parts, and wear and tear. Ensure all safety features are functioning properly and that operators are well-trained in the operation process, safety procedures, and potential dangers. Always wear personal protective gear, such as safety glasses, hearing protection, and gloves. Keep the work area clean, tidy, and well-lit, and secure the workpiece firmly in place.
Milling vs. Cutting
Milling involves cutting with rotating tools that pass over a part, precisely removing material to form the desired shape. Cutting, as a standalone process, typically involves a broaching action with linear motion to remove an elongated kerf, resulting in a slot that separates the material. While the distinction between milling and cutting can be blurred, milling cutters are often used for simple cutting jobs, whereas linear cutters are not typically used in milling operations.
Milling vs. Swiss Machining
Swiss machines, early versions of multi-axis machining centers, were developed for mass-producing clocks and watches in the 19th century. The addition of cutter rotation allowed the production of flat and square features on cylindrical workpieces. It wasn't until the 1970s that lathes began to incorporate these combined features, and the development of 6-axis CNC machines has truly competed with the functionality of Swiss machines
.