Time to read: 6 min
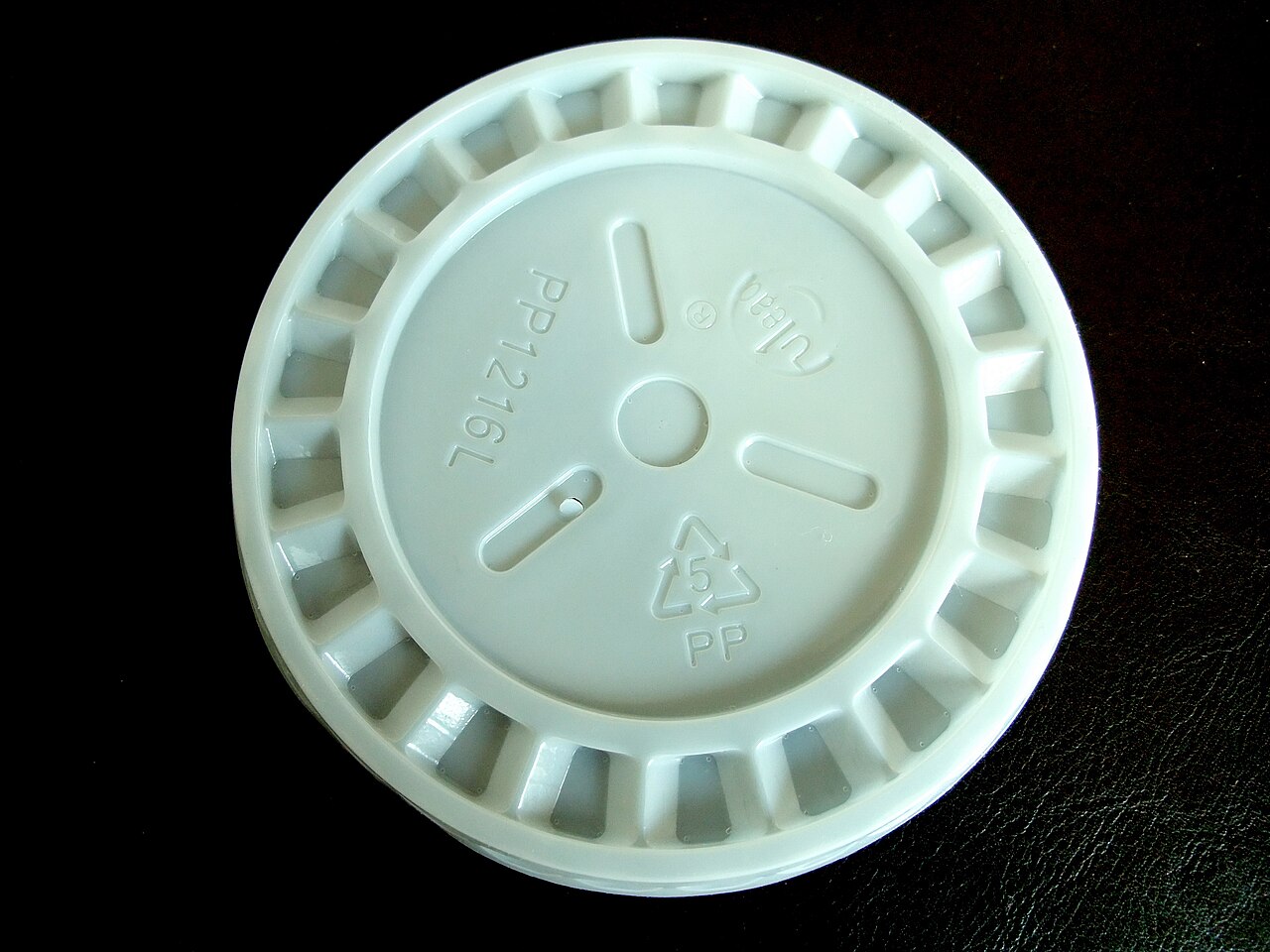
Understanding Polypropylene: Production and Applications
Polypropylene is a semi-rigid, cost-effective, and durable thermoplastic polymer that offers excellent resistance to chemicals, electricity, and fatigue at high temperatures. It is considered a hazard-free plastic, making it suitable for producing a wide range of products, from plastic furniture and machinery to pill containers and syringes. Despite its versatility and strength, polypropylene also has some disadvantages, such as its susceptibility to oxidation, high flammability, and sensitivity to chlorinated solvents and aromatics. This article explores how polypropylene is made, its uses, and its advantages and disadvantages.
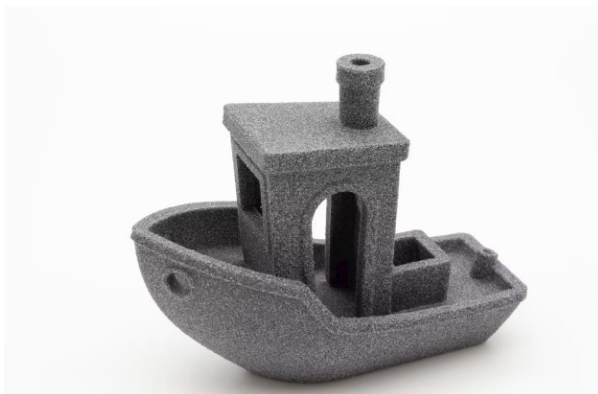
What is Polypropylene?
Polypropylene (PP) is a low-density, stress-resistant thermoplastic derived from a propene (or propylene) monomer. The chemical formula for this linear hydrocarbon resin is (C3H6)n. Discovered in the mid-1950s by Italian scientists, it is now the second most manufactured plastic after polyethylene.
As a thermoplastic, polypropylene can be heated to its melting point, cooled, and reheated without significant deterioration. This property, along with its ability to liquefy instead of burn at high temperatures, makes it a popular choice for manufacturing processes like injection molding. Other key characteristics include:
- Chemical Resistance: Polypropylene is resistant to diluted bases and acids, making it ideal for containers that hold liquids such as cleaning solutions.
- Toughness: It has elasticity over a limited deflection range and is considered tough due to its early plastic distortion in the deformation process.
- Insulation: It has high electrical resistance, making it suitable for electronic components.
How Polypropylene is Made
Polypropylene is produced by polymerizing propylene gas using a catalyst system, typically a Ziegler-Natta or metallocene catalyst. The polymerization parameters, including temperature, pressure, and reactant concentrations, are set according to the desired polymer grade. The manufacturing methods can occur in either gas-phase or liquid-phase processes:
- Gas-Phase Process: The reaction occurs in a fluidized bed reactor at temperatures of 70°C to 100°C and pressures of 1-20 atm. Propylene is converted to polypropylene as a fine powder, which is then separated from unreacted propylene and hydrogen using cyclone separators. The powder is then pelletized and ready for further use.
- Spheripol Process: This process uses propylene, ethylene, and hydrogen to produce polypropylene. The reaction happens by suspending the catalyst and monomer units in an inert solvent. The polymer is then stored for later use.
Primary Uses of Polypropylene
Polypropylene is utilized in various industries, including:
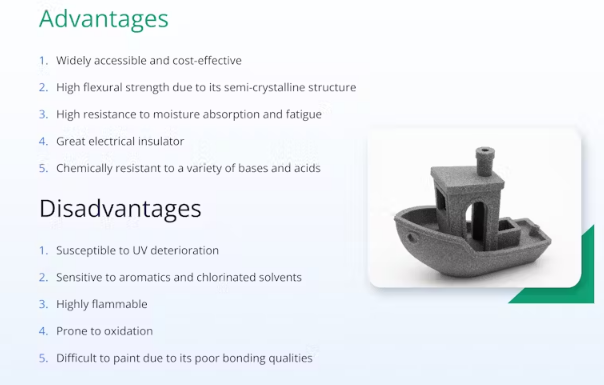
- Material Handling
- Packaging
- Medical Devices
- Clothing
- Car Parts
- Housewares
- Toys
The packaging industry often uses polypropylene as a substitute for paper and cellophane due to its low cost and flexibility. It is used to make pallets, bottles, jars, yogurt containers, hot beverage cups, and food packaging. In the automotive industry, polypropylene is used for batteries, bumpers, instrument panels, and interior elements. Its resistance to chemicals, bacteria, and steam sterilization makes it suitable for medical applications like disposable syringes, diagnostic devices, and pill containers.
Injection molding is the most common manufacturing process for polypropylene due to its rapid response to injection speed and pressure, allowing for high production rates.
Advantages and Disadvantages of Polypropylene
The advantages of polypropylene include its strength, low cost, and versatility. However, it is prone to oxidation and has high flammability. Other advantages and disadvantages are detailed in the infographic below.
Comparative Analysis
- Polypropylene vs. Polystyrene: Polypropylene is sturdier and has better chemical resistance compared to polystyrene, which is more brittle and less resistant to certain chemicals.
- Polypropylene vs. Polyester: Polypropylene is more water-resistant and less expensive to manufacture than polyester, but polyester offers better UV and heat resistance.
Conclusion
Polypropylene's flexibility, durability, and chemical resistance make it a valuable material in many industries, with the packaging industry being its primary user. While it is considered safe for human health, it can deteriorate under prolonged exposure to UV rays or high temperatures. Unofactory specializes in polypropylene injection molding, offering expert solutions for your manufacturing needs. Get a quote on your designs today!