Time to read: 6 min
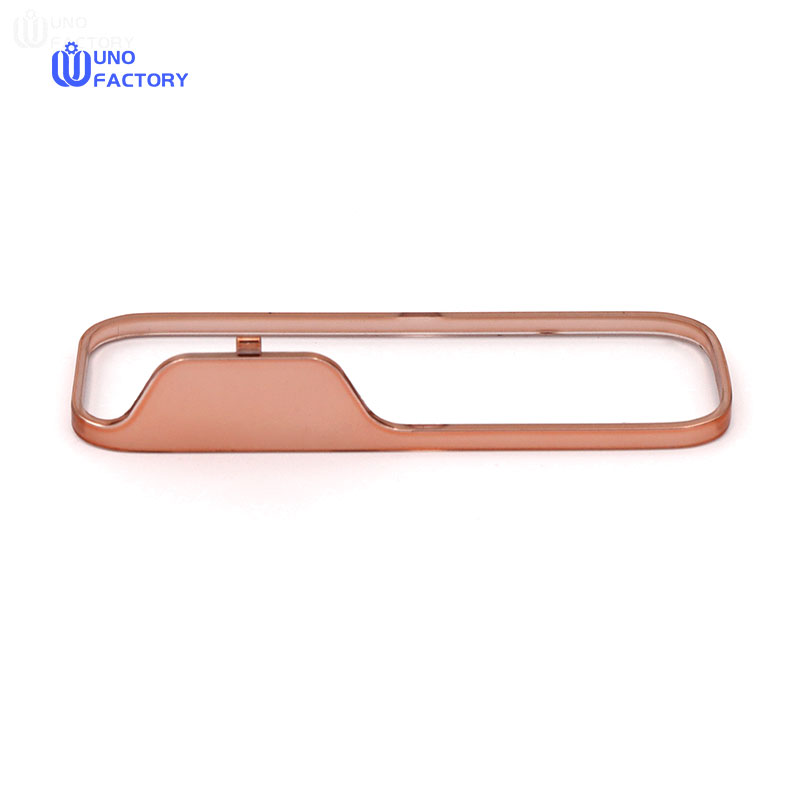
ABS injection molding is a widely used manufacturing process that involves injecting molten ABS plastic into a mold cavity under high pressure and temperature. This technique is prevalent in the automotive, consumer products, and construction industries for producing various components and products. This article will explore the definition, uses, process, and techniques involved with ABS injection molding. Discover how UnoFactory leverages this process to deliver high-quality ABS components.
What is ABS Injection Molding?
ABS (acrylonitrile butadiene styrene) injection molding is a standard method for producing ABS plastic products. ABS is a strong and lightweight thermoplastic polymer that is easy to work with. The process involves adding molten ABS into a mold cavity and then removing it after it cools. It's a fast and cost-effective method used to craft ABS products at an affordable price. It's a popular choice for household appliances, tools, and medical devices. It's used to make Lego bricks, computer keyboard keys, power tool housings, and power outlet fittings, and in the automotive sector, it's used for dashboards, seat belt parts, door trim, and bumpers.
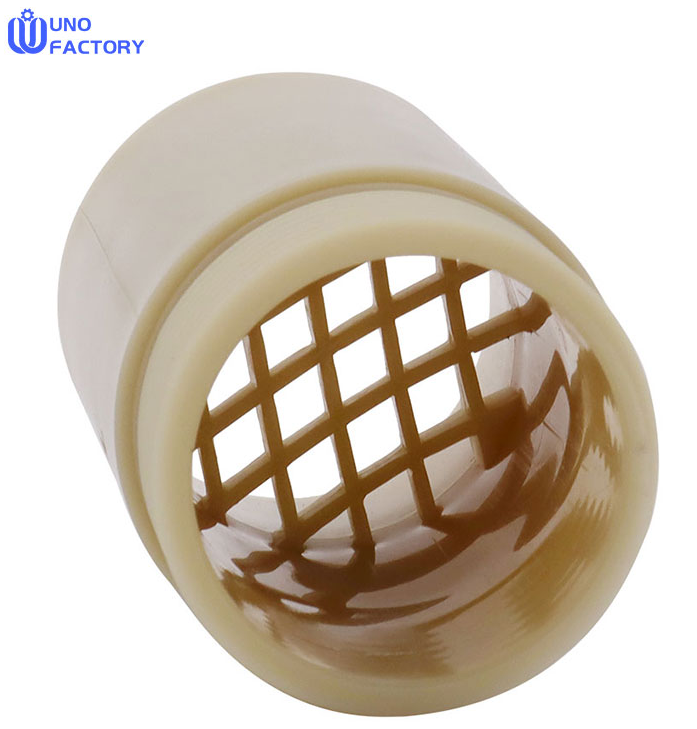
Understanding the ABS Injection Molding Process
The ABS injection molding process is similar to that of other thermoplastics. Resin pellets are fed into a hopper, where they are melted and injected into a mold using high pressure. Once the plastic cools and re-solidifies, it is removed from the mold. This simple and efficient process is ideal for high-volume production and generates very little waste.
Design Considerations for ABS Injection Molding
The intricacy of the parts you can make is only limited by a set of well-established DFM (design for manufacturing) guidelines. ABS injection molding can produce multi-featured, complex parts with metal inserts or overmolded soft-grip handholds. The process allows for easy color customization and minimal human intervention, keeping labor costs low and making the parts more affordable.
Properties of ABS
ABS is easy to shape, recyclable, resistant to chemicals and heat, and has a low melting temperature. However, it is not ideal for prolonged exposure to UV light and outdoor elements. To enhance its durability, ABS can be painted or electroplated with metal.
Technical Considerations
- Viscosity: ABS's viscosity increases when heated past its plasticizing temperature, requiring careful temperature control, especially for thin-walled components.
- Cooling and Shrinkage: Uneven cooling can cause warping or shrinkage, which can be mitigated by using molds with evenly spaced cooling channels and high gate pressure.
Injection Molding Techniques
Different techniques are used depending on the part's requirements:
- Thin Wall: Increased pressure is needed for thin-walled parts, and molds must be designed to handle this pressure.
- Large and Hollow: Water- or gas-assisted injection molding helps create even thickness and smoothness in large, thin, or hollow parts.
- Thick Wall: Compression injection molding can be used to reduce internal stresses and manage sink marks.
- Multi-Material: Techniques like insert molding or overmolding are used for components made from various materials.