Time to read: 6 min
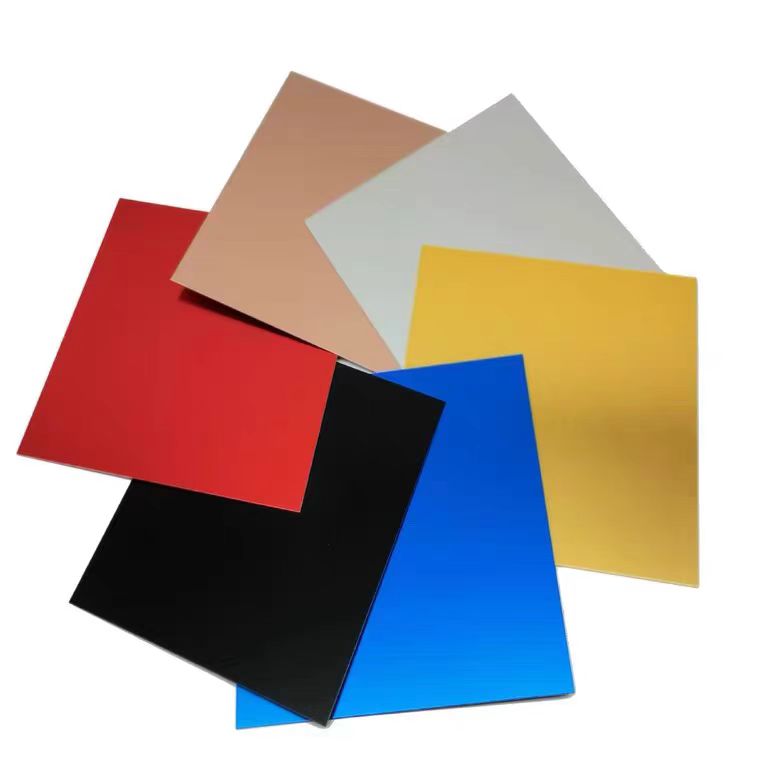
What is Anodized Aluminum?
Anodized aluminum refers to the aluminum that has undergone an anodization process, resulting in a durable, corrosion-resistant oxide layer on the surface. This process not only protects the aluminum from wear and corrosion but also allows for a wide range of colors to be applied to the surface, enhancing its aesthetic appeal.
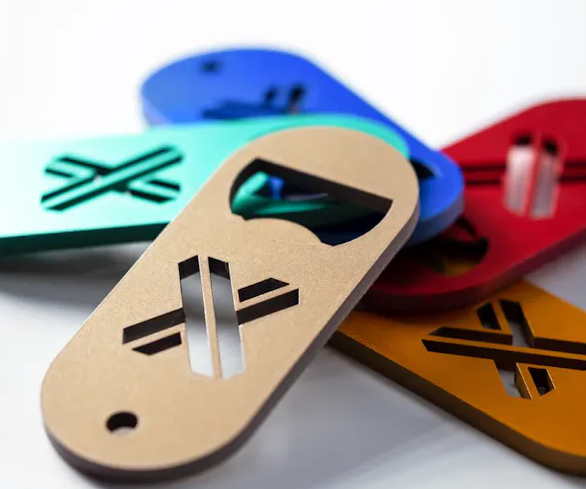
The Process of Anodization
The anodization process involves submerging the aluminum component in an acidic electrolyte solution and passing an electric current through it. This causes the aluminum surface to oxidize, forming a layer of aluminum oxide. The thickness of this oxide layer can be controlled, and it is this layer that gives aluminum its enhanced properties.
Achieving Colors in Anodized Aluminum
One of the most striking features of anodized aluminum is its ability to display a variety of colors. The colors are achieved through the interaction of light with the oxide layer. While the oxide layer itself is typically clear, certain processes can introduce color. The colors can range from classic brushed aluminum looks to more vibrant hues.
Applications of Anodized Aluminum Colors
Anodized aluminum colors are used in a wide range of applications due to their durability and aesthetic appeal:
- Architectural Features: Anodized aluminum is used for facades, window frames, and other architectural elements that require a durable and attractive finish.
- Automotive Industry: Components such as trim pieces, badges, and interior components benefit from the protective and decorative qualities of anodized aluminum.
- Consumer Electronics: Many electronic devices use anodized aluminum for their casings, providing a sleek look and added protection against scratches and wear.
- Aerospace Industry: The corrosion resistance and strength of anodized aluminum make it ideal for use in aircraft components.
Benefits of Anodized Aluminum Colors
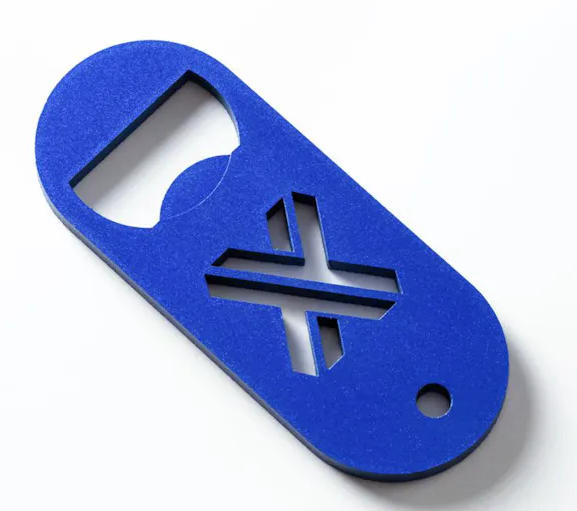
The benefits of using anodized aluminum colors include:
- Enhanced Durability: The anodized layer provides a protective barrier against corrosion and wear.
- Aesthetic Appeal: The range of colors available allows for customization and branding opportunities.
- Environmental Resistance: Anodized aluminum is resistant to various environmental factors, including UV rays and chemical exposure.
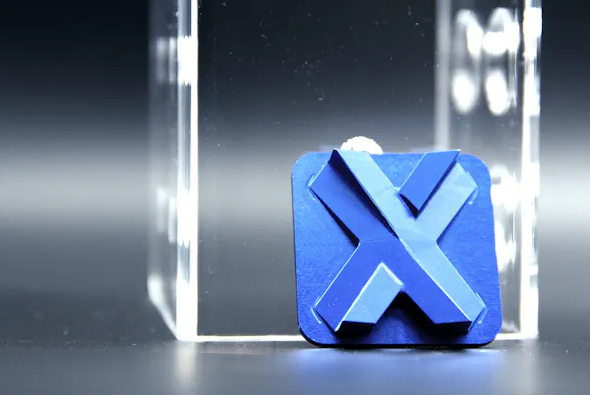
Summary
Anodized aluminum colors offer a combination of functional and aesthetic benefits, making them a popular choice in many industries. At UnoFactory, we specialize in anodizing aluminum to meet the specific needs of our clients. For more information on how UnoFactory can assist with your anodized aluminum color requirements, contact us today.
Disclaimer
The content provided is for informational purposes only. UnoFactory makes no representation or warranty, expressed or implied, regarding the accuracy, completeness, or validity of the information. Performance parameters, geometric tolerances, specific design features, quality, and types of materials, or processes should not be inferred to represent what will be delivered by third-party suppliers or manufacturers through UnoFactory’s network. Buyers are responsible for defining the specific requirements for their parts. Please refer to our terms and conditions for more information.